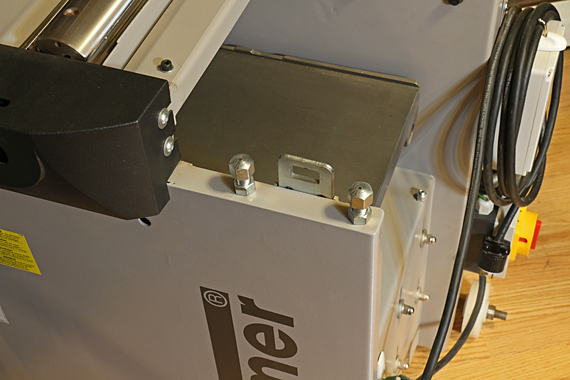
Lots of information can be found on this website about jointer-planer combination machines and the Hammer A3-31 in particular. I have received many inquiries, especially regarding setup and adjustment of the Hammer. One thing that I have not covered in detail is how to make the infeed and outfeed tables parallel to each other along their lengths. This is quite doable but not simple.
Let us first set the context. As described in detail here, there are several logical steps to adjusting the jointer. In summary:
1. Start by verifying the flatness of the tables.
2. The width of the outfeed table is then made parallel to the cutterblock
3. The arc of the cutting blades must be consistently adjusted relative to the outfeed table. Here is a practical and accurate method applicable to most machines.
And here are the nuts and bolts on the A3-31.
4. The infeed table and outfeed table are then made parallel across their widths by adjusting the infeed table. Step 4 here describes the details, including for the Hammer.
5. And now for the tricky part. The infeed and outfeed tables must be made parallel along their lengths.
For reasons similar to wanting a hand jointer plane to have a flat sole, so should the machine tables be adjusted. In my opinion, this adjustment should be done with a one-sided tolerance. Aim for the tables to be parallel, but a trace of convexity, like the letter “A,” is OK, but there should be no valley, like the letter “V.”
So, how is this done on the A3-31? In those earlier posts, I referred to “geometry” without presenting the details. You could work hit-or-miss to make the adjustment, but with four points of adjustment involved, it would probably be unnerving and cause you to give up, and then tolerate using a poorly adjusted jointer, which will in turn wreak all sorts of ugly havoc on your ensuing work. So, really, it is worth deciphering my geometric method. It works.
I attached my handwritten notes, made years ago. Click on the little picture below for a full-size version.
The front-side adjustment bolts are shown in the photo at the top of this post.
The hinge-side adjustment screws are found under this plate:
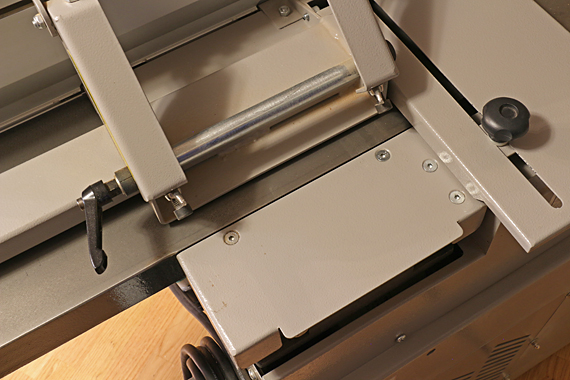
The pencils are pointing to them:
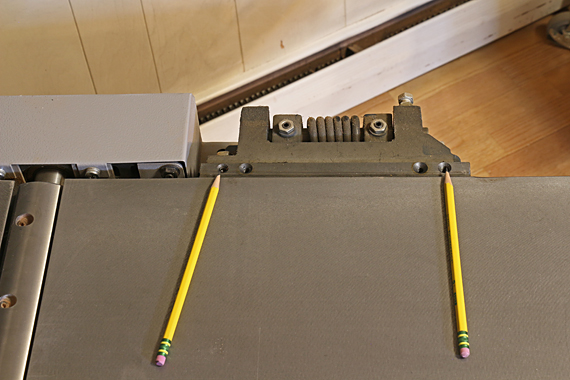
These bolts must be both be loosened to allow the set screws to move:
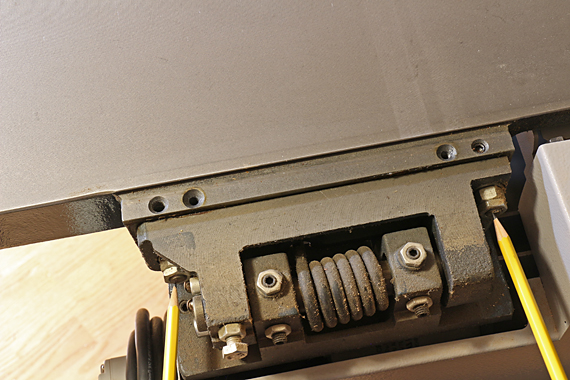
The method starts with placing a straightedge to extend the full length of the infeed table with a sufficient amount to also have a good register on the outfeed table. The infeed table starts low and then is adjusted upward to the first touch on the straight edge. If you have done all the previous work as described above, the place of the touch will tell you how the tables are aligned. In my machine, the tables were delivered tilted toward each other, like a “V,” so the first touch of the straightedge was at the outer end of the infeed table.
Measure the gap as shown in my notes. Note then that I have simply diagrammed similar triangles among the straightedge-table and the pairs of adjustment screws, and calculated the amount of adjustment to be made at the appropriate screws. I then converted that into how much to turn each screw based on the thread pitch.
OK, I think you can see why I did not include this in my original set of posts! It is a bit painful. I like math so I admit to a bit of joy in working this out, but for those A3-31 owners not so disposed, contact me and I’ll try to help.
Thankfully, the machine holds its adjustments very well.