The #4 bench plane, about 9 1/2″ long with a 2″ wide blade, is probably the most popular smoothing plane among woodworkers, and will be the focus of this discussion. Some prefer the maneuverability of the smaller #3, and some like the added weight and 2 3/8″ blade of the #4 1/2, but all of these bevel-down smoothers can be used in several configurations to effectively work a range of easy to difficult woods. It is a matter of employing various strategies.
Strategy #1: Choose a 50° frog.
Bevel-down smoothers are, unfortunately, usually configured with a 45° frog as standard. Lie-Nielsen’s great planes are available with 45°, 50°, and 55° frogs. Other brands, such as Clifton, Wood River, and Anant, do not, to my knowledge, offer this important choice.
Why 50°? This will smooth tame woods, such as plain walnut and poplar, about as well as a 45° frog. In some cases, the 45° frog can produce a slightly more cleanly severed surface, but the difference is nearly imperceptible and, in most cases, a very sharp blade negates any practical difference between the two.
Yet, wonderfully, for most moderately figured woods, a high-quality #4 with the advantage in reducing tearout of the 50° frog, along with a properly prepared blade and chipbreaker, is all you need. I do not want the expense and hassle of changing frogs, and the 50° is more versatile than the 45° or 55°. Furthermore, with the alterations discussed below, a higher attack angle can be created without changing out the 50° frog.
This presupposes a well-tuned, high quality plane. To digress somewhat, here is a partial list of important features:
- The sole must be flat in the key places, especially at the toe and around the mouth.
- The frog should be accurately machined and of good design, such as Lie-Nielsen’s, and adjusted to create a tight mouth, just enough to pass thin shavings without congestion.
- The blade must be properly cambered. How much camber? Ideally, shavings under 0.001″ thick should feather out to nothing toward the sides of the blade edge.
- The chipbreaker should be set close to the blade edge. How close? Well, it depends on the wood, the chipbreaker edge design, and the thickness of the shavings you are taking, so you must experiment a bit. About 1/64″ gap is a starting point.
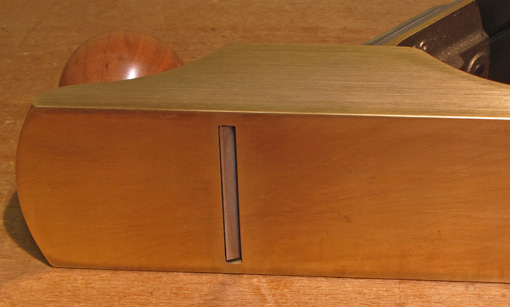
So, there are two corollary tips:
- Taking thin shavings means taking lots of passes, which leads to using a duller blade, unless the wood surface is properly trued beforehand. In other words, use your smoother only to smooth, and as little as possible. Set the surface up with your truing planes.
- Consider an O-1 steel blade for most of your smoothing in moderate woods. It is easier to sharpen and shape, and probably can be made sharper, than A-2. It will likely dull faster though, or maybe just differently, so it will need touch ups.
Strategy #3: When the going gets tough with mean and nasty woods, try raising the attack angle by using a back-beveled blade.
I keep a separate blade for my #4 with a 10° bevel on the back (the “flat” side). Because this setup is used in tough woods, the abrasion resistance of A-2 steel is an advantage, and the back bevel facilitates sharpening. With the 50° frog, this creates an attack angle of 60°, which is a big advantage in eliminating tearout. It is much like having a separate plane with a 60° frog, which you therefore do not need.
The back bevel needs only to be very narrow since it is really just the first tiny bit of blade that matters – the first several thousandths, probably, that are involved in severing the fibers. At the sharpening bench, I use a magnetic angle gauge, in conjunction with a strip of wood on the stone, to make a reproducible back-bevel angle. The front-side bevel should not be too steep; 25° is plenty, creating a total bevel of 35°. More than that and the blade “wedge” will be too thick and, I feel, offer too much pushing resistance in the wood. The chipbreaker cannot be set as close to the edge with a back bevel but that does not matter as much due to the high attack angle.
Going higher than a 60° attack angle, by whatever method, does not seem to make planing go better, even in very difficult woods. The cutting action becomes more like scraping. I find that the best course of action for those situations is to simply use a scraping plane or hand scraper.
In summary, with one high-quality, well-tuned bevel-down smoothing plane, with one frog, and two well-prepared blades (three is a luxury), you are equipped to venture into smoothing lots of wonderful woods.
Of course, there are more options, and they too work. Next: Bevel-up strategies.