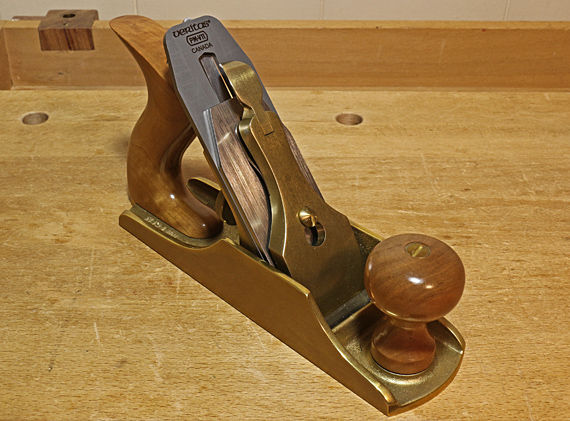
Will the PM-V11 blades made for Veritas standard bevel-down bench planes work in a Lie-Nielsen plane? These are nominal 1/8″ thick blades, the same thickness as the L-N blades. I am not referring to Veritas PM-V11 blades made for “Stanley/Record planes,” which are .100″ thick (a little more than 3/32″).
Manufactured by Lee Valley/Veritas, PM-V11 is a wonderful steel that I’m glad to have in my Veritas bevel-up planes. Veritas offers lots of information about it, including their extensive testing, in a dedicated website.
First, here are my impressions from using PM-V11 blades in my LV BU planes. Though obviously not scientific, they differ somewhat from Veritas’ testing.
For ease of sharpening, Veritas found PM-V11 about the same as A-2 but, as we would expect, not nearly as easy as O-1. My sense is that PM-V11 is actually noticeably easier to sharpen than A-2. I don’t think it actually wears faster on my CBN grinder, diamond bench stones, and 0.5 micron ceramic finishing stone, but somehow I feel more confident in creating a reliable final sharp edge. This is completely subjective and perhaps is just a matter of how the steel feels on the stones.
As to the sharpness of a new edge, it’s hard to beat O-1 but I think A-2 can get pretty close. PM-V11 seems to me to be even closer to O-1, and probably equal. Again, this is subjective and perhaps is more of a matter of ease and reliability in getting to a pristine final edge.
Regarding edge retention, it seems odd that the Veritas testing found that A-2 barely beat O-1. With the caveat that A-2 blades vary considerably, I think most woodworkers find as I do that A-2 holds its edge significantly longer than O-1. My unscientific sense is in general agreement with the extensive Veritas testing that the edge in a PM-V11 blade indeed outlasts most A-2, though not by as wide a margin as Veritas found. I think the Hock A-2 blade that I have in my jack plane would give PM-V11 a run for its money. Still, you’ve got to respect the extensive testing that Veritas has done.
In short, there is good reason I’d like to use PM-V11 in my bevel-down Lie-Nielsen planes, which are, of course, absolutely fantastic planes.
In my L-N #4, the lateral adjustment button measures .445″ across. The slot in the L-N O-1 blade that I own is .455″ wide, and .452″ in my L-N A-2 blade. The slot in the Vertias PM-V11 was .441″ when I received it.
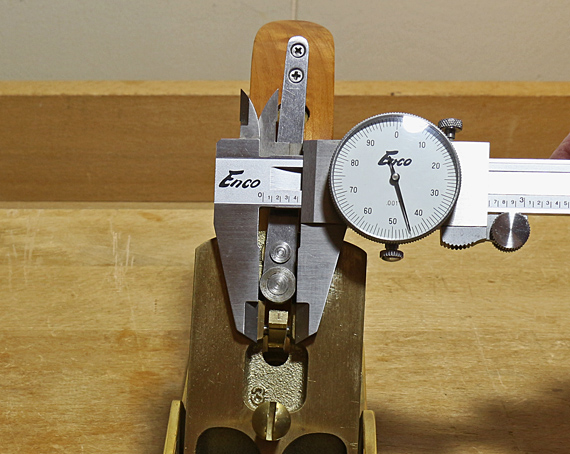
I simply widened the Veritas blade slot to .446″ using a 2″ x 6″ DMT extra-coarse diamond stone and cleaned up the resulting harsh edges with the other (coarse) side of the stone. Though this results in just minimal clearance of the slot around the adjustment button, the blade beds just fine. In fact, the reduced play in the lateral adjustment mechanism makes it a bit more responsive.
The Veritas PM-V11 and Lie-Nielsen blades are virtually identical in thickness (within one thou) at about 1/8″. There is no need to compromise by using a thinner blade. There is also no problem connecting the chip breaker, nor with the fit and function of the blade advancement pawl. The slot in the Veritas blade is longer than in the L-N blade but that does not matter as far as I can tell.
I think now I’ve got the best of both of these great companies in my good old #4.
How bad was opening the slot?
Any issues with the engagement of the depth adjust into the cap iron? You are about .020 closer with this setup.
Nice to have that option. Even nicer would be if there was an option to buy the planes new with a choice of blade like LV does. I’ve been very pleased with my PM-V11 blades.
Steve,
Easy work. I put the blade lengthwise in my scraper vise (former saw vise), stuck the diamond stone through the slot and held it at each side, using lengthwise strokes, keeping the stone square to the blade. The x-coarse diamond cuts fast.
The new blade does not change the relationship (in any axis) of the chipbreaker with the depth advancement pawl. No problems.
Yea, it looks like L-N now offers their planes with any blade steel that you want as long as it’s A-2. As much as I am a big fan of the L-N company, I wish they had more options.
Rob
I thought the LN blades were .140 thick and the LV is .125.
You can see the effect of this by putting a thin stanley iron of .080 or less in your LN plane. The chipbreaker (LN) won’t seat all the way on the adjusting pawl. .015 thickness difference isn’t enough to cause a problem apparently.
If only there was a strong market for LN A-2 irons.
As noted in the post, the LN and LV blades are both 1/8″ thick. They are within one thou of each other at about .126.
L-N #2, 3 ,4, and 5 use nominal 1/8″ (.125″) blades. L-N #6 and 7 use .140″ and the giant #8 uses .170″.
You beat me to it!
I didn’t realize they used different thicknesses for different sizes. I have only one LN, which is a 4-1/2 so I was seeing things through a .140 lens.
Apologies for skimming over the .001″ part of your post.
No worries, Steve, I appreciate your interest and comments. For a more complete rendering, I should have pointed out in the post that all of the LV standard bench planes use 1/8″ blades, and some of the LN bench planes use thicker blades:
#2, 3, 4, 5: .125″
#4 1/2, 5 1/2, 6, 7: .140″
#8: .170″
Rob
Good info. Just for grins, have you tries the thicker blade in a Stanley?
Does the yoke end reach?
Hi Larry,
The only Stanley plane I own is the #20 compass plane with a 3/32″-thick Hock blade and 1/8″-thick Hock chipbreaker, and it works just fine. In my Record jack plane, nearly 40 years old, is a 3/32″-thick Hock blade and a 1/8″-thick Veritas chipbreaker, and that also works fine.
If you want to use PM-V11 in your Stanley plane, note that Lee Valley sells .100″-thick blades designed to fit. http://www.leevalley.com/us/Wood/page.aspx?p=42607&cat=1,41182,43698&ap=1
For my LN #4, I wanted to keep the full OEM 1/8″ thickness but in PM-V11, and so I did the modification of the LV 1/8″-thick blade that they use in their standard bench planes, as described in the post.
Rob
Hi Rob,
I’m curious what you thought about the behavior of PM-V11 as it dulls.
In my experience A2 tends to chip at the edge, leaving telltale ridges in the planed surface, while O1 dulls much more smoothly.
Did you notice that PM-V11 dulls one way or another?
I used to detest sharpening my LN A2 blades on diamond stones using the grits Paul Sellers uses (coarse, fine, super fine). I broke down and bought an XX Coarse diamond stone and start with that on my LN A2. Problem completely solved. Somewhere between 50 to 100 strokes and I have a good burr. Then similar number strokes on each stone.
Hi Bill,
PM-V11 seems to dull more like O-1, though not as fast, of course. Good A-2 really has little tendency to chip at the edge if the secondary bevel is high enough, say 32-33 degrees. Problem is, some A-2 is just crappy and seems to chip no matter how it is sharpened. http://www.rpwoodwork.com/blog/2017/08/13/a2-steel-plane-blades-are-not-all-the-same/
Hi Joe,
Good that you found a method that works for you, as we all must! I form the primary bevel with the CBN wheel on my Tormek machine, then go to diamond bench stones, and then the Gukomyo 1/2 micron ceramic stone.
Rob
A couple of months ago, I tested until reasonable failure (which I defined as failure of a plane to keep itself in the cut without additional downforce) the following irons in beech:
* An O1 iron that I made (harder than LV’s), I later tested it against a hock O1, and both failed at about the same point
* V11
* CPM 3V
* A2 (Lie Nielsen)
* CPM M4
* Tsunesaburo blue steel
* A chinese almost-M2 blade (we had the iron analyzed, and it’s a cheap version of M-2, a little short on some of the alloying elements, but it’s close).
what I found was a surprise (I thought that the 2 to 1 claim from veritas seemed to be a bit rosy) on one case, and not in another.
First – the non-surprise: I started the test with hard maple, but twice stalled because of mineral inclusions. In each case, the mineral inclusions caused every single iron to sustain halting damage (nothing is tough enough to get through it).
And the surprise: O1 is within about 20% of A2, The tsunesaburo iron lasted about the same length of time as good O1 steel (again, not soft, probably 62-63 hardness). 3V was somewhat better than A2, and the chinese HSS was about the same, and V11 and powder M4 were nearly identical – planing twice as long as the LN A2.
The other surprise – the surface was brighter off of V11 than it was off of carbon steel, otherwise V11 showed similar behavior (tiny defects may come and go, but they sort of “heal” themselves by getting worn off uniformly. AND, the planing effort (all irons except 3V were able to be used in the same plane) from V11 was less than anything else in the test. It was noticeable. M4 had the most planing resistance (we really don’t know why).
All of the completed tests except for one were done in american beech, the longest of which lasted more than 4000 feet of planing (depending on the board, planed distances were around 2000-4000 feet until a plane failed to keep itself in the cut with a shaving of 2 1/2 percent. I rotated the irons every 200 feet planed so that no plane gained an advantage, and weighed the shavings to make sure they were doing an equivalent amount of work per stroke. And then took microscope pictures of the edges at each rotation.
I’m uncompensated, just curious. There’s a bunch of post history on woodcentral, and eventually I’ll manage to get it organized and published somewhere.
Long story short – if the wood is dirty or very abrasive, it really doesn’t matter what the iron is – sharpening faster is key. If the wood is clean and the cut smooth (something akin to planing material just out of a machine planer prior to finishing, or cleaning up a machine jointer edge), V11 does show in testing to last twice O1 and almost twice A2. While it attains a good edge pretty easily sharpening, it does grind about half as fast on a power grinder as O1, which can create heat issues. Thankfully, it is not a high speed steel, but the tempering schedule makes it so that mild overheating has almost no effect on hardness.
During the process, I planed somewhere around 40,000 feet.
It’s important to state again, I’m uncompensated, and thought that the test may expose LV’s claim as too rosy.
I have since planed some rosewood guitar necks with the alloy that V11 is likely made from (i’m also an amateur toolmaker) and noticed some damage to the edge, so before I finish publishing everything I found testing, I will be getting the V11 iron back out and testing it in rosewood against O1 to see if the relationship still holds.
As a matter of cross referencing knife makers – we found (I received some assistance in terms of guidance about materials and metals research from a couple of other enthusiasts) that knife slicing durability tests in rope are a pretty good proxy for plane iron durability….anyway, we also found the metal suspected to be used for V11 fared very well in knife slicing tests.
I’m more of a traditionalist as far as tools go, but my metal jointers and smoothers have all been switched over to V11 or irons I’ve made from the suspected alloy.
Wow, thanks David for sharing these results from your extensive efforts.
My casual observations about PM-V11 are consistent with your testing. It’s good stuff. I’d add that it seems to need a higher secondary bevel angle than O-1, for which somewhere in the mid to high 20s, maybe 30° at most, is fine. I’ve had the best results with PM-V11 durability with at least 30°, better about 32°, for most plane blades.
I’d also add that it’s hard to test A-2 against other steels because A-2 is so variable – among manufacturers, among different blades from a single manufacturer, and even among successive sharpenings of a single blade. However, I do think a good A-2 blade does last a lot longer than O-1. My favorite A-2 is Hock.
Thanks again,
Rob