• Sunday, September 26th, 2010
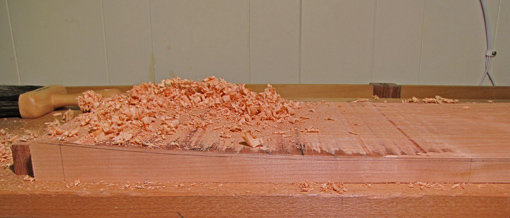
It’s really not fair that I say that about wood. After all, I am forever cognizant of one of the first few sentences of Bruce Hoadley’s Understanding Wood : “Wood evolved as a functional tissue of plants and not as a material designed to satisfy the needs of woodworkers.” We cannot cut down the tree, cook the wood, and expect it to do just what we want.
Understanding is indeed the key to a successful relationship with wood as we work with what it is, rather than what we might wish it to be. One of the prime reasons a project can fall short of expectations is the failure to anticipate insidious changes in the wood.
For the top board of a cherry wall cabinet, I wanted a lengthwise curve in its thickness to produce an appealing motif borrowed from the Japanese torii gate. Starting with rough stock nearly 1 ½” thick and about 9″ wide, the final thickness at the center of the 25″ length will be just under 11/16″ and, at the outer ends, just under 1 3/16″, for a curve depth of ½”.

A simple approach would be to joint and thickness the rough board to a bit more than 1 3/16″, then cut and smooth the curve on one face. Done, right? Wrong. Removing a substantial thickness from one side of a kiln-dried board is almost sure to distort it, transforming the opposite flat face that was previously true into a potato chip that will wreak havoc with subsequent attempts at joinery.
We know from resawing wood that most boards retain some internal stress from casehardening. This usually causes the halves of a resawn board to cup toward the inner face. This is not always the case but there is a test for it. This is not a problem of moisture exchange. (Though that could also be present as another issue.) The stresses present in the dried wood cause it to occur even in a board with uniform moisture content through its full thickness. The distortion happens immediately after the board is resawn.
The photos below show the offcut within minutes after sawing. The outside face was flat before sawing. With that face placed on the table saw top, it can be seen that the piece has curved toward the inner (sawn) face in both along its length and across its width.
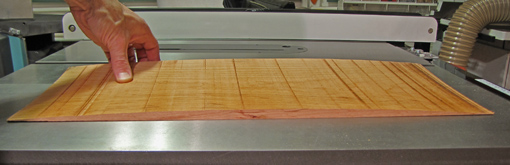
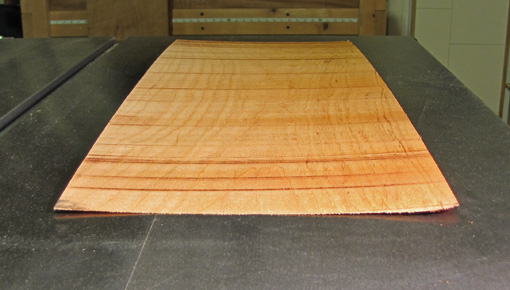
I’ve left out some steps which I will show in the next post. With this board, I did not have much extra thickness to work with after getting past the rough sawn surfaces, so I needed to anticipate what the wood had in store and have a good plan going in. I will detail the solution in the next post, though I think most readers will be one step ahead of it.
• Saturday, September 11th, 2010

Before using this unimposing little plane I was doubtful that it could get much work done but having put it to work in the shop I am convinced that it really performs. It brings an effective combination of toughness and control to curved work and hollowing.
The plane has a bevel-up A2 blade bedded at 20̊ and a 3 1/2″ long double convex sole with a shallow 27″ radius along its length and a steeper 3″ radius across its width. The blade is secured with a simple cap and thumbscrew mechanism and is adjusted by hand or by tapping with a small hammer. Nothing complicated with this tool, it goes right to work.

The “squirrel tail” handle is the key to controlling the plane. The dome of the tail nestles in the lower part of the palm of the hand while the fingers surround the plane’s body with the index finger settling on the round depression at the front of the tool. This allows one to adjust and balance hand pressure toward the front or back of the tool as needed in order to engage the blade to cut on a curved surface. I find this makes it easier and more natural to control than other convex sole tools such as a spokeshave.
The mouth opening is quite wide which, along with the curved blade, and lightweight handiness of the plane, allow quick back and forth strokes, much like the action of a scrub or jack plane. I find this tool is best used as a sort of mini jack plane for hollowing. The photo below shows an example.
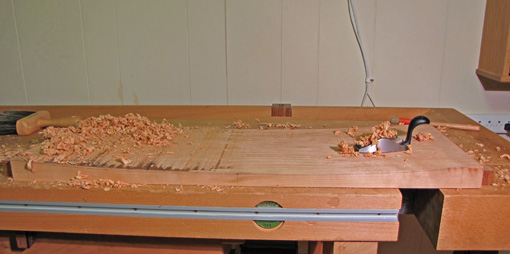
I bandsawed a shallow lengthwise curve into a 27″ long piece of plump 5/4 9″ wide cherry which will be used as the top of a wall cabinet. I used the convex sole plane to efficiently remove the bandsaw marks and refine the curve. The plane felt like an extension of my hand allowing me to work intuitively as I formed the curve to my liking. The shallow scallops that remained were easily removed first with a curved Surform rasp followed by an Auriou curved “ironing rasp,” hand scraper, and sandpaper.
[I will mention that removing a substantial portion of wood from one side of a board like this is likely to create problems as the internal stresses in the board become unbalanced. I plan to discuss in a future post how I anticipated and worked around this sneaky problem.]
While I’m very happy with the L-N convex sole plane and recommend it, I would consider some design changes if I could have my preferences. It is a bit undersized for medium scale work, although an increase in size might sacrifice some of its handiness. A slightly larger radius across the width of the sole would suit more of my work. Perhaps a choice of sizes and soles could be made. Finally, knurling or a coarse surface on the widest parts of the sides would allow a better finger tip grip. I guess I can add that myself.
This tool review is unsolicited and uncompensated.
• Thursday, September 09th, 2010
Thank you, Heartwood blog readers
I started this blog two years ago believing that woodworkers have a lot to gain from sharing information and ideas in this format. That belief has been reinforced, the readership has grown far beyond anything I anticipated, and there has been much gracious and encouraging feedback. This is not a farewell, just a juncture at which to say, “Thank you,” dear readers.
Of course, you have a wealth of choices in the internet woodworking world, so I am very appreciative of the time you spend here in this little corner of it. I hope the Heartwood blog has advanced your woodworking and spurred your enjoyment of it.
I will continue to present thoughtful, useful content. The topics arise from the sawdust and shavings of my shop, devoid of hype and armchair pretenses. The writing will continue to be largely technical though often laced with reflections and sentiments that accompany my woodworking.
If you are even slightly inclined, do leave comments on the posts, please. Other readers and I would like to hear from you. I must continue to hold all comments for approval because even though the Akismet program filters out many thousands of spam comments, some do find their way through.
So far I’ve posted about 45,000 words and 200 photographs, enough to fill a nonfiction book. This is a labor of love and I can only say that I hope to continue to be able to devote the time.
For now, thanks for reading and happy woodworking!
Rob